Centrifugal Spark arrestors for dust collection
Review
Description
Centrifugal Spark arrestors for dust collection Detail:
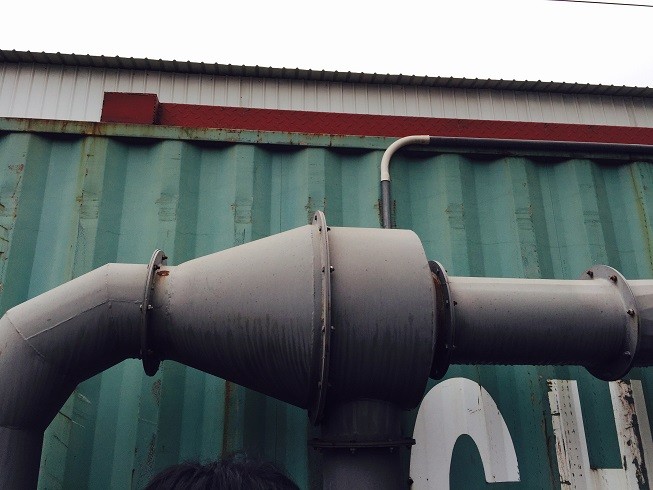
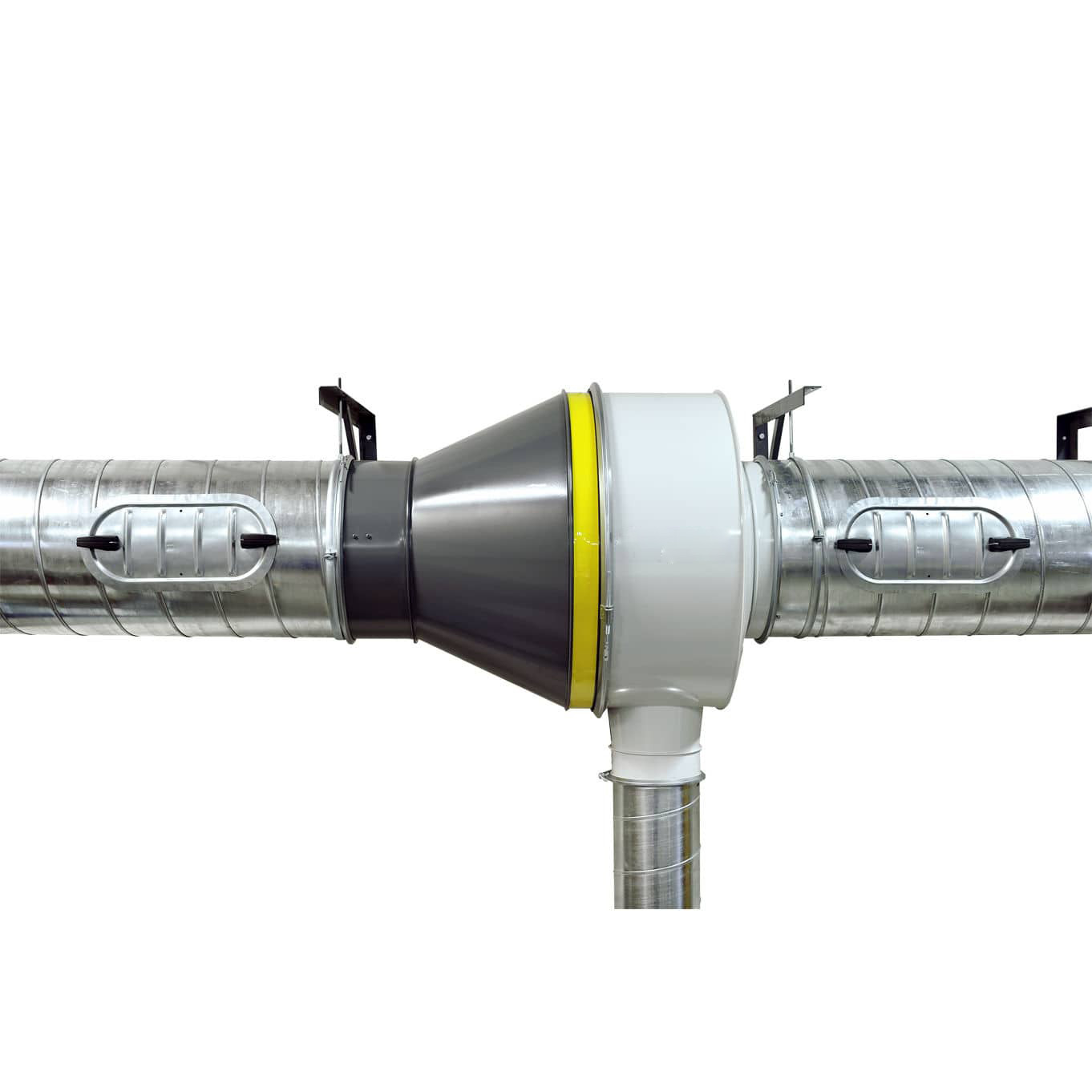
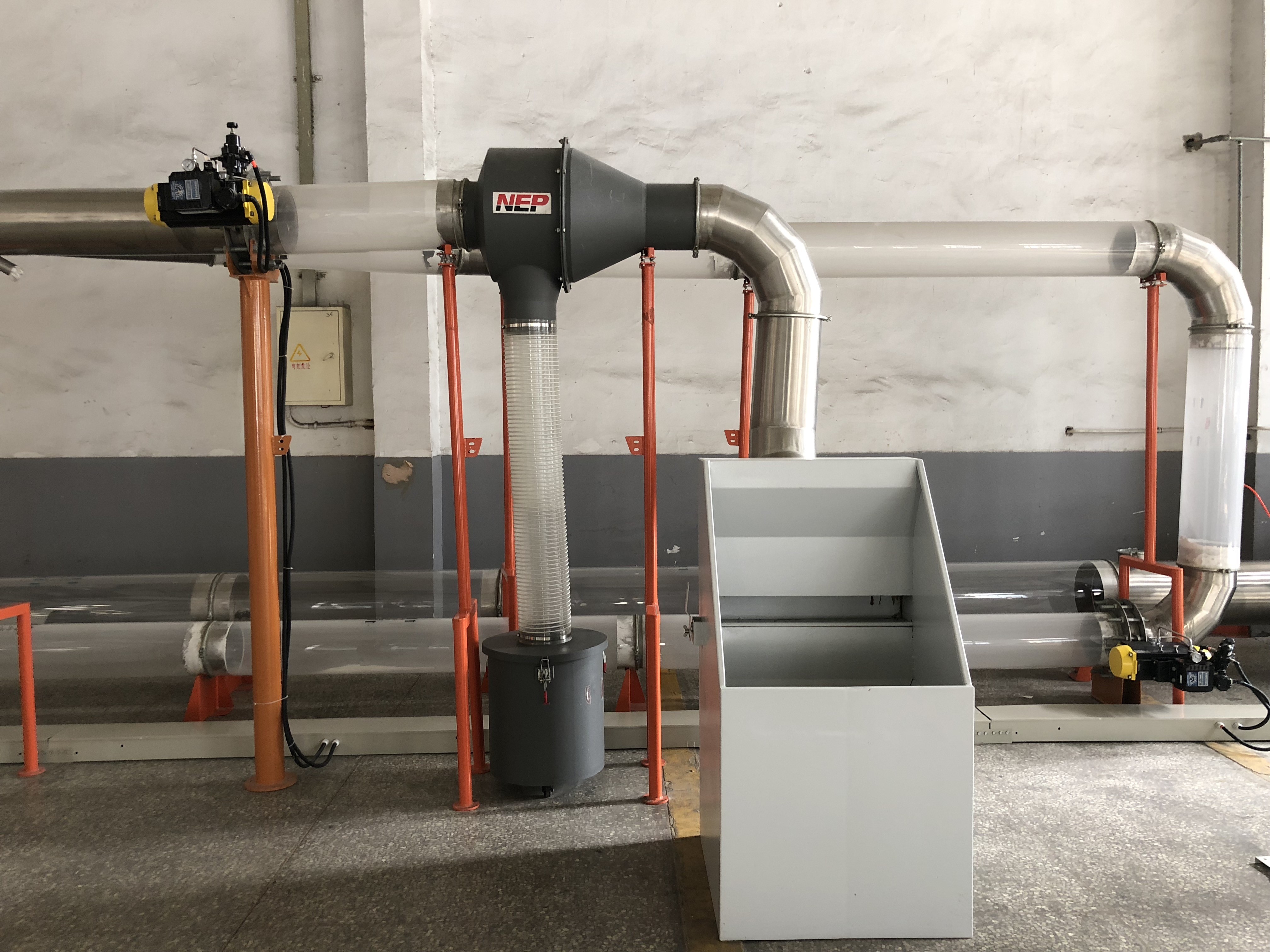
• Feature:
The spark arrestor (or spark arrester) is a device that prevents the emission of Flammable sparkle dust from combustion sources into the dust collector whose filters are bags, polyester cartridges, or sinter-plated filters. The small spark posed a super hazard to dust explosion or fire disaster.
Centrifugal spark arrestors make up with stationary vanes to trap down high gravity sparks or particles by centrifugal force. In other words, Centrifugal forces throw the sparks against the wall of the arrestor, where they are separated then pull through filters.
The exhaust spark arrester sometimes is considered as a horizontal cyclone for powder separation or recycles especially for the high gravity dust. Some customer uses this spark trapper as a pre-collection for high-density dust. Further more, some dust with oils is also can be trapped to protect the terminal equipment (attention: please consider the duct safety in explosive atmosphere).
• WHAT IT DOES:
• Cools and arrests sparks without water or chemical injection
• Reduces burn-damage to filter media
• Reduces duct and dust collector damage
• Destratifies temperature and cools local hot spots
•SPARK MITIGATION:The Spark Cooler is ideally suited to mitigate sparks generated in metal and other low-load material processing applications, under non-explosive conditions. The Spark Cooler works to create turbulence in the air flow stream, thereby disturbing the thermal bubble surrounding the spark and allowing the lower temperature in the gas stream to influence the particle temperature. It is not an extinguishing system and should never be applied as a standalone device in processes requiring absolute spark suppression.
• Application:
Extinguishes and cools sparks / burning embers from welding fumes, plasma cutting table, grinding, polishing, buffing, belt sanders, furnaces, biomass boilers, and any application which creates a possible spark hazard.Robotic welding of oily stamped products; Robotic and automatic welding of oily products;Manual welding of oily products.
Position: lazar cutting machine.
Dusts contain: oils, cutting fume, spark, carbon, and carbon steel…
Function: spark trap before into the dust collector.
Working feedback: without this equipment, the bag house burned before, after use it, no risk of fire hazards.
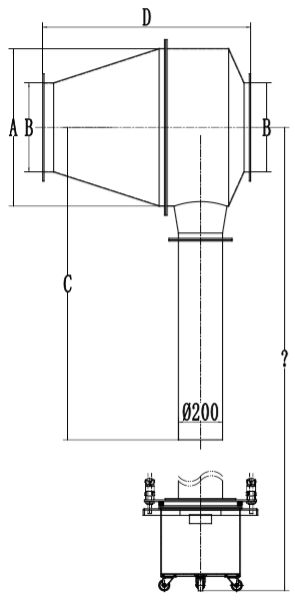
SPECIFICATION PARAMETER
SC-200 | SC-250 | SC-300 | SC-350 | SC-400 | SC-450 | SC-500 | |
A(mm) | Φ400 | Φ500 | Φ600 | Φ680 | Φ710 | Φ820 | Φ900 |
B(mm) | Φ213 | Φ250 | Φ300 | Φ350 | Φ400 | Φ450 | Φ500 |
C(mm) | Min.400 |
Min.500
|
Min.600 | Min.650 |
Min.680
|
Min.750
|
Min.800
|
D(mm) | 670 |
778
|
860 | 905 |
943
|
1050
|
1159
|
Airflow (m3/h) | 1200-1800 |
1800-2800
|
2800-4000 | 4000-5500 |
5500-7000
|
7000-9000
|
9000-11000
|
Resistance(pa) | ≤1000 |
≤1000
|
≤1000 | ≤1000 |
≤1000
|
≤1000
|
≤1000
|
OPERATION PRINCIPLE
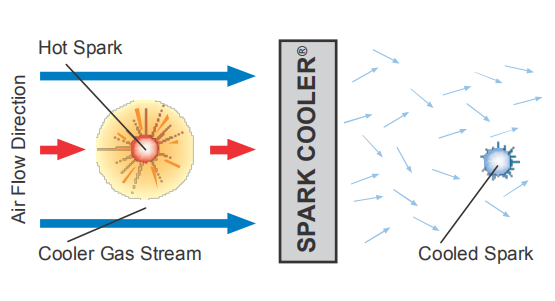
PRODUCT FAQ:
Q: What it does?
A: • Cools and arrests sparks without water or chemical injection
• Reduces burn-damage to filter media
• Reduces duct and dust collector damage
• Destratifies temperature and cools local hot spots
Q: What is the normal application?
A: The Spark Shield is a safety solution and recommended to be used in applications with a high risk, such as:
• robotic welding of oily stamped products
• robotic and automatic welding of oily products
• manual welding of oily products
• cutting tables
• schools and other areas with risk of cigarette butts
• All Metal Process Industries • Fabrication facilities
• Automotive plants
• Foundries
• Metal Recycling
• Robotic weld cells
• Battery Recycling
• Ball Bearing Manufacturing • Charcoal manufacturing
• Shoe grinding (rubber) • Coffee manufacturing
Q: What is the selection procedure?
A: Step 1: Identify the duct diameter.
Step 2:Confirm the air flow. If the flow falls outside the range shown, refer to the flow information below.
Step 3:Identify the corresponding model number
Step 4:Select the material and flange pattern.
Q: What are the Performance Advantages
A: • Proven Spark Mitigation
• Greatly reduced damage to filter media
• Minimal pressure drop
• Zero footprint/space requirement
• Easy installation: no factory tech or calibration required • Works in vertical or horizontal position
• No secondary dust accumulation point
Contact Email: Info@dustscrubber.com
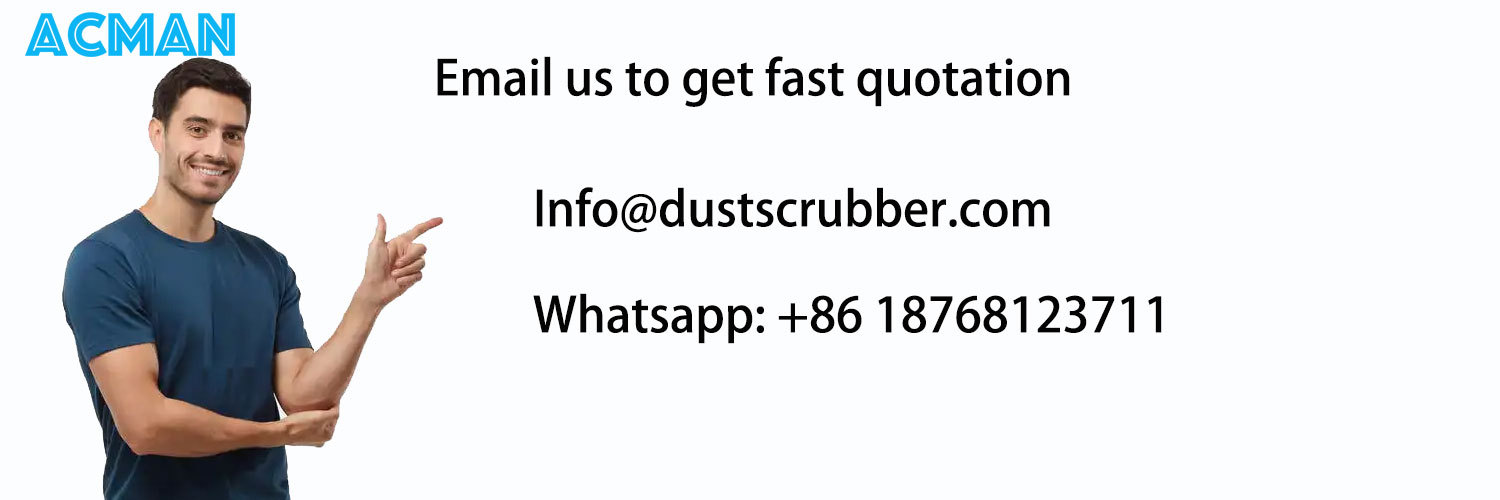