Discuss of Dust Removal in Solid Agent Production Workshop
- Share
- Issue Time
- Jun 17,2022
Summary
Among more than 5,000 pharmaceutical preparation manufacturers in China, there are solid
The manufacturers of pharmaceutical preparations account for more than half of the population.
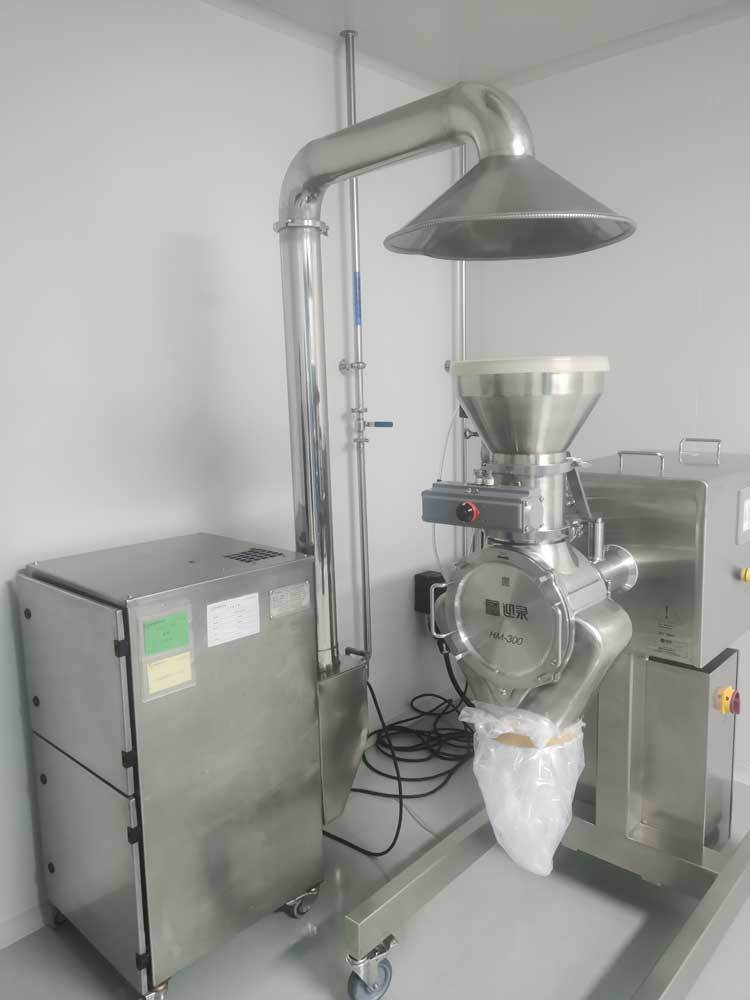
Discuss of Dust Removal in Solid Agent Production Workshop
Among more than 5,000 pharmaceutical preparation manufacturers in China, there are solid
The manufacturers of pharmaceutical preparations account for more than half of the population. It can be said that solid
Body preparation is a common dosage form in my country's pharmaceutical production enterprises. for medicine
As far as the solid preparation purification workshop of the factory is concerned, the powder cattle pollution in production is the
the most prominent feature. Weighing, crushing, sieving in the production of solid dosage forms
Granulation, drying, whole granulation, blending, tableting, capsule filling, granulation
In various processes such as packaging, dust flying and diffusion are most likely to occur, especially
Mixing or cross contamination occurs by purifying the air conditioning system. for the strong
Toxic, irritating, allergic dust, the problem is even more serious.
Therefore, the drug dust emitted in the solid preparation production workshop is subject to
Effective capture, control, and removal are essential in the production of solid dosage forms.
important issues that must be addressed. In this paper, the solid preparation purification workshop powder
The links and causes of sitting are briefly analyzed, and Dingfen is proposed
Some measures for dust control and removal are provided for your reference.
Links and causes of dust generation in solid preparation purification workshop
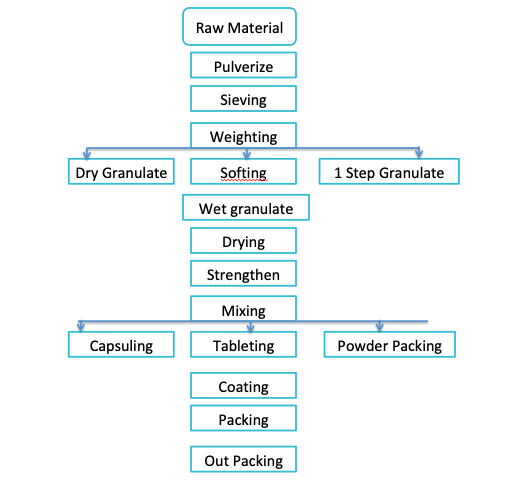
Protect the weighing device with a curtain, the effect is better, and the solution can be better
Solve the problem of dust generation during weighing.
Granulation: Existing granulation methods usually include thousand granulation, wet granulation
There are three types of granulation and one-step granulation. Dry granulator is developed in recent years
It is a new type of pharmaceutical equipment that uses the crystal water of the material itself to directly
Then dry and extrude into granules. Thousand method granulator is a closed structure,
It can effectively prevent dust from flying during pellet operation, but it can effectively prevent dust from flying during feeding and discharging.
It is also inevitable to generate more dust during operation. Wet granulator
It is convenient, fast, less dust flying, and can be used for dense testing, but it is
There will also be a lot of dust flying when feeding.
One-step granulator integrates mixing and granulation
The drying process is operated in a clean airtight container under negative pressure
work, the powder flying is less, and the double capture system is generally used to make
There is less powder in the finished granules, but also during feeding and unloading operations
more dust
Whole granulation and blending: usually, the granules after granulation and drying are rectified.
After the granulator is granulated, it enters the next step of the mixing process. Pharmaceutical companies now generally use
The fast granulator used has less dust during the production process, but the
There will be a lot of dust flying field when feeding. If true is used in the mixing operation
The material can avoid the generation of dust when feeding, but there will be more problems when unloading.
dust is generated.
Capsule filling, tableting, granulation: blended granules
Made by capsule filling machine, tablet press and granule filling machine respectively
semi-finished products. Existing domestic commonly used capsule filling
High frozen tablet machine adopts closed structure. and equipped with a vacuum cleaner
Effectively prevent dust flying in the production process. If on the refill day
The use of vacuum feeding can minimize the generation of material during feeding.
dust.
Coating: The most efficient coating machines are currently used. usually
The air system is equipped with a vacuum cleaner, and the entire coating operation is carried out in a closed container.
Yes, the dust will not contaminate the coating room. But the general public
During the operation of the washing machine, due to the friction and tumbling between the films, a large
dust.
It can be seen from each link of the above solid preparation production that
Choose a more advanced
"GMP" required production equipment,
It can effectively prevent the generation of dust during the production process, but in each
During the feeding, discharging and equipment cleaning of the sequence, there will still be
of dust produced
3 Dust removal measures in solid preparation purification workshop
As mentioned above, in the production of solid dosage forms at various stages
It is easy to fly and spread dust in the air, especially by purifying the air conditioner to
Mixing or cross contamination occurs. Therefore, it is necessary to
Effectively capture, control and remove dust between
The measures taken for dust control and removal generally include the following four:
Physical isolation, in-situ exclusion, differential pressure isolation and fresh air full exhaust.
3.1 Physical isolation measures
In order to prevent the dust from flying and spreading, it is best to use the
Barriers to isolate, should not wait until the dust has spread throughout the room
To ventilate and dilute, the consequences of that can only be twice the result with half the effort. king of things
It is also suitable for occasions where local dust removal cannot be achieved for the dust source, for example
The dust source equipment has a special shape, and the dust catcher cannot be installed.
Physical isolation within the range.
3.1.1 Isolation method
There are generally three ways of physical isolation: in-situ isolation
Side isolation and independent isolation. In-situ isolation: dust generating equipment is located in
That is, it is isolated with a barrier in place in one corner, as shown in Figure 2(a):
Leave. If the equipment is arranged along the wall, the whole side wall is separated from the whole room.
As shown in Figure 2 (6): Independent isolation: only one device in the whole room
And the equipment is not to the side or corner, you can use physical barriers to
Enclose it to form a hut, as shown in Figure 2 (c, for example, weighing poison
Industry is an example of independent isolation.
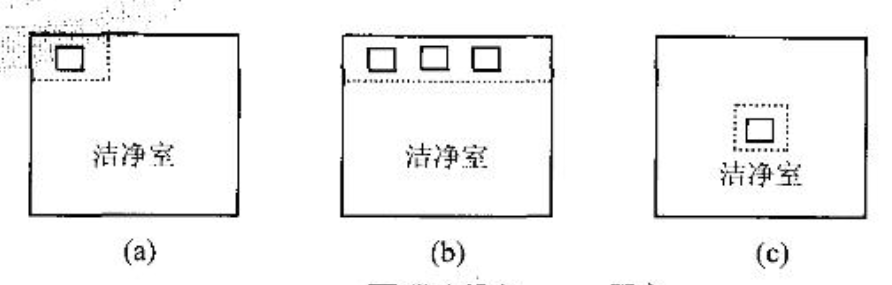
3.1.2 Purification scheme
After physical isolation measures are taken, air purification solutions can have
The following three:
①The production process of isolation has considerable requirements on air cleanliness:
In this case, clean air can be sent to the high-altitude area to achieve a certain cleanliness level
In addition, set up a stage punching room in the high-altitude area, and the stage-punching kiln and the high-altitude area remain the same
The cleanliness is different and its pressure is higher than that of the workshop outside the high bay area.
②The production process in the isolated area does not require high air cleanliness:
In this case, an independent exhaust can be set up in the height area. outside the high-altitude area
The air in the workshop enters the high-rise area through the air vents on the physical barrier.
If the amount of occurrence is not large, it is not necessary to open the air vent, and enter through the terminal or louver.
Wind will do.
③ The isolation area requires a large amount of exhaust air: in this case, it can be
In order to send the exhaust air in the high-altitude area back to the high-altitude area after passing the raw material and passing through the pool,
That is to form a self-blessing ring. What should be specially explained here is the dedusting and passing pool device
s position.
As shown in Figure 3(a), the stand-alone generator and process equipment are placed in the same
One room is the most common way. However, this method is simple and easy to implement,
However, due to the low efficiency of this type of dust collector, the empty space of the production workshop is discharged.
The air contains a high concentration of bio-energy, so the common air outlet should be equipped with sub-high-efficiency
Or high-efficiency tools can be used.
As shown in Figure 3(6). It is a special eliminator installed on the production car of Weijin
In the detoxification room, this method can reduce noise and shadow, and avoid dust removal.
The dust collector caused secondary pollution to the workshop due to improper cleaning, but the opening of the dust collector
Stopping will affect the air balance of the room.
As shown in Figure 3(c), the entire dust chamber is used as an exhaust
The negative pressure room is provided with an air outlet with a filter on the partition wall, regardless of the
The start and stop of the dust collector will not affect the air flow balance in the southern room.
In the case of a large exhaust air volume in the isolation area, if this
Partially exhausted from the outside workshop. will greatly increase the large system
cooling, heating and purification loads. If the dust collector is used deeply
The way that the gas passes through the port efficiently and then is used by the decoration ring can greatly reduce the overall
The energy consumption of the workshop can be saved, and the operation cost of the clean room can be saved. According to Wang Fuguo
The waiting room is divided into a solid preparation purification workshop with an area of 1000m°.
Do not dial two schemes (one is to use the return air after treatment, the other
It is a comparison of the full exhaust air of the dust-generating workshop), we can see that:
The scheme of using return air can reduce the economic operation cost by 39,000 yuan per year, saving
Save 18% of operating costs. therefore. Under the premise of meeting GMP,
An energy-saving dust removal system solution should be selected as much as possible.
3.2 Local risk elimination measures
3.2.1 Installation of external dust catchers
For physical isolation, dust-laden air should be excluded. But push in situ
The exclusion of the application is because some processes, if isolated, will not affect the operation zone.
It is inconvenient to come, and it is easy for adult students to install external traps at local locations.
dust list, local exclusion measures can be adopted, that is, the installation of external traps
dust hall,
Since the external trapping green is installed on the upper part of the dust source or at the bottom
The total size and installation position should be
Please refer to Figure 4 for the test." In order to avoid the influence of lateral airflow, the mask mouth
The housing stock should not be too high. Its height H is as small as possible less than or equal to the hand 0.34
(The size of the long side of the single port), at this time, the exhaust air volume of the biocide is calculated as follows:
L=KPHVx m's

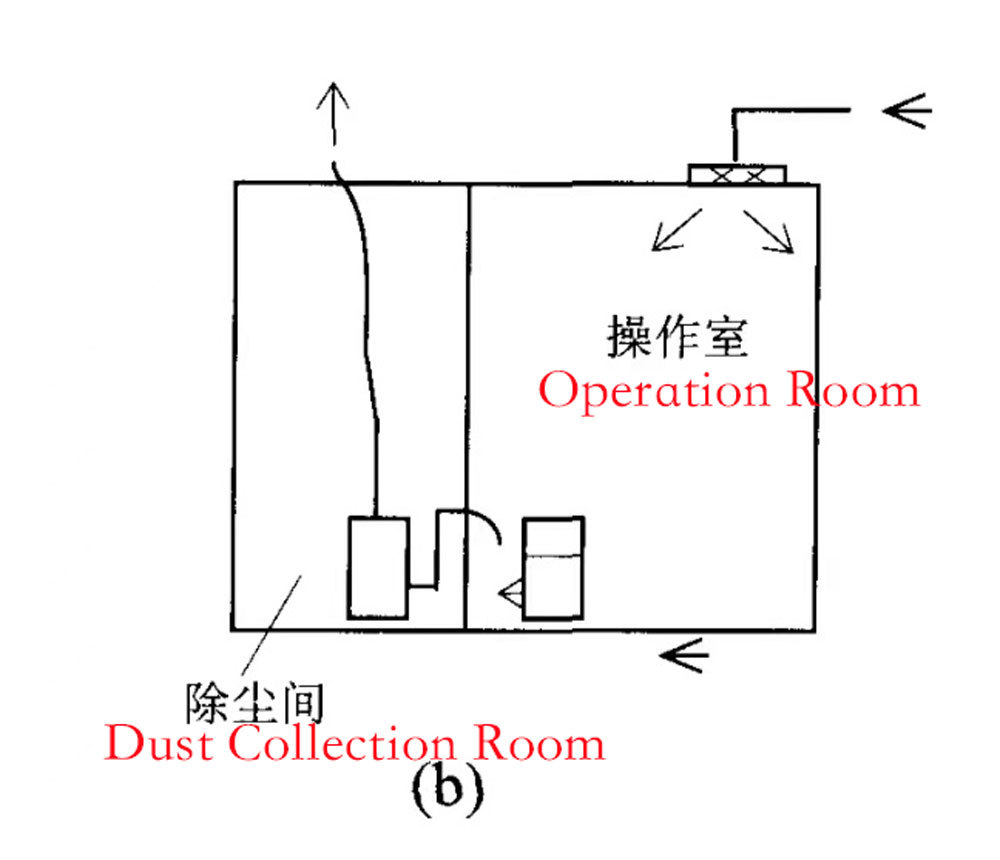
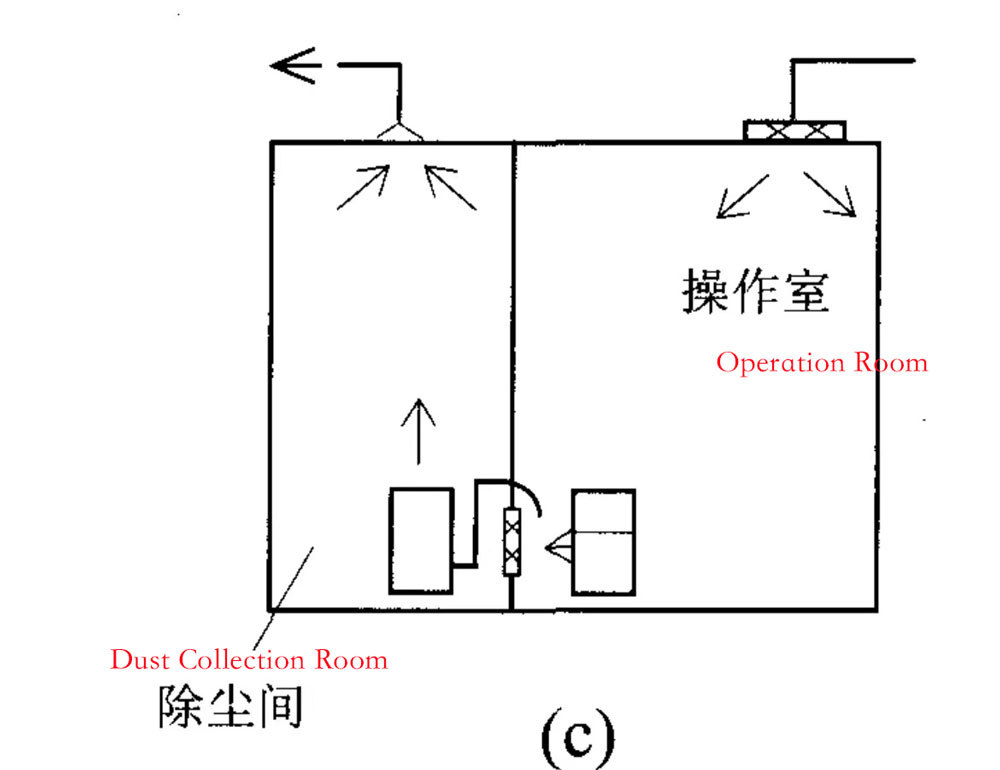