The Application of the Sinter-plate filter in the Hot Roling Mill Production Operating Mode
- Share
- Issue Time
- Jun 18,2020
Summary
The sinter-plate filter technology is a revolutionary breakthrough in dust collector technology. As a new generation of highly efficient powder collector,it is better than traditionary collector because of many especial advantages.
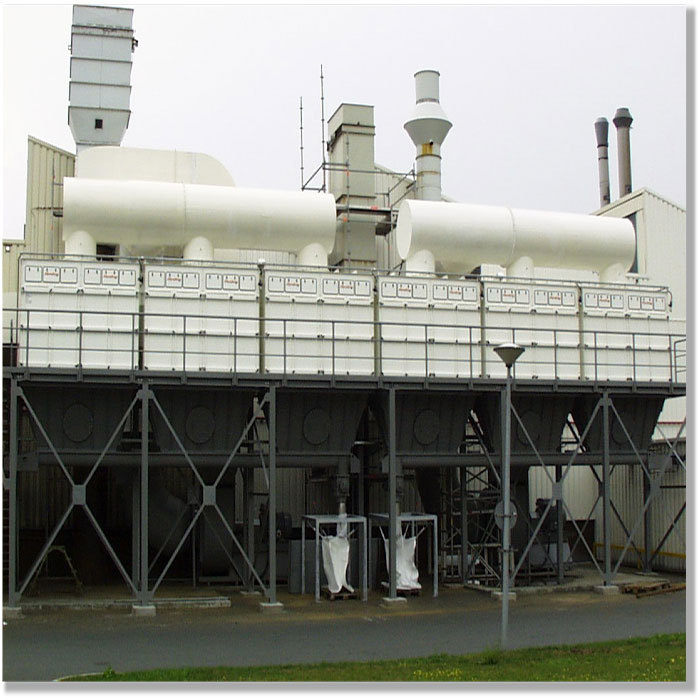
The birth background of sinter-plate dust collector
At present, the dust collectors that realize gas-solid separation in industry are mainly divided into 4 categories: machinery type dust collector, wet type dust collector, electrostatic type dust collector and filter type dust collector.
The temperature of the filter material used in the dust removal of the commonly used cloth bags is generally below 250~C. If the temperature of the dust is higher, the cooling measures must be adopted.
This will not only lose most of the energy, but also complicate the system. In the ultra-fine dust working condition, the dust concentration at the entrance of the bag dust collector is much lower than the powder concentration used for the ultra-fine powder trapping operation, and it is easy to cause the dust collector to be overloaded and the fine powder to leak out during use If you collect a powder containing a certain amount of water, the phenomenon of sacks often occurs. It is difficult to control corona under high temperature and high pressure. Wet dust removal will produce a large amount of sewage, which requires secondary pollution treatment.
Therefore, the collection of ultra-fine dust requires a collector with good effect and strong adaptability.
Plastic burning board dust collector is a new generation of high-efficiency ultra-fine powder collector used in industry since the 1980s and 1980s. It has unique advantages in filtering ultra-fine dust.
Performance of sinter plate dust collector
1.Strong ability to capture ultra-fine powder
Sintering board filter is a new type of filter material used in industry since the 1980s. The surface is coated with a PTFE layer. After a special process, uniform micropores are formed inside, with a pore size of 30um and a surface pore size of up to 1um, so the filtration accuracy is very high. The dust collection efficiency for dust above 1um is as high as 99.99%. After air filtration, the mass concentration of dust is less than 20 mg/m 3 and basically achieves zero emissions.
Sintering board filter is a new type of filter material used in industry since the 1980s. The surface is coated with a PTFE layer. After a special process, uniform micropores are formed inside, with a pore size of 30um and a surface pore size of up to 1um, so the filtration accuracy is very high. The dust collection efficiency for dust above 1um is as high as 99.99%. After air filtration, the mass concentration of dust is less than 20 mg/m 3 and basically achieves zero emissions.
2.Rigid wave porous structure design
The sinter plate filter element is made of a variety of polymer compound powders and special binders by casting and sintering to form a wave-shaped porous matrix as the substrate of the plastic-fired filter element. The thickness of the substrate is about 4mm, and the interior is 30um. Uniform pores, then fill the FTFE in the voids on the surface of the matrix through a special spraying process to form pores of about 1-2 um.
The sinter plate filter element is made of a variety of polymer compound powders and special binders by casting and sintering to form a wave-shaped porous matrix as the substrate of the plastic-fired filter element. The thickness of the substrate is about 4mm, and the interior is 30um. Uniform pores, then fill the FTFE in the voids on the surface of the matrix through a special spraying process to form pores of about 1-2 um.
3.Constant pressure drop
Since the sinter board dust collector is filtered through the PTFE filter layer on the surface, the smooth surface makes the dust difficult to stay. In theory, even a small amount of very fine dust enters the gap can be set by pulse dust cleaning compressed air (provided that The pressure meets the actual requirements) Blow away, there should be no clogging in the filter plate, as long as a short time passes, the pressure of the filter plate tends to be stable. Therefore, the dust collectorResistance does not change with time, ensuring process stability.
Since the sinter board dust collector is filtered through the PTFE filter layer on the surface, the smooth surface makes the dust difficult to stay. In theory, even a small amount of very fine dust enters the gap can be set by pulse dust cleaning compressed air (provided that The pressure meets the actual requirements) Blow away, there should be no clogging in the filter plate, as long as a short time passes, the pressure of the filter plate tends to be stable. Therefore, the dust collectorResistance does not change with time, ensuring process stability.
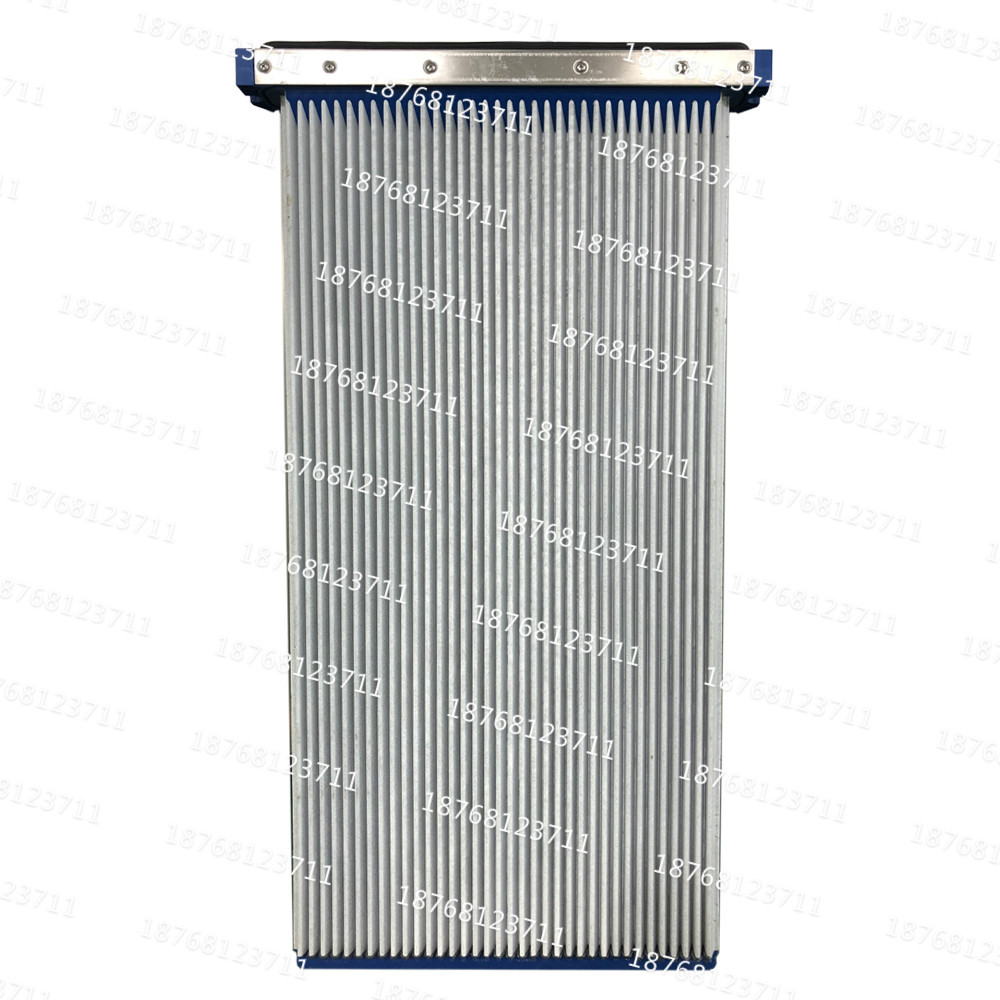
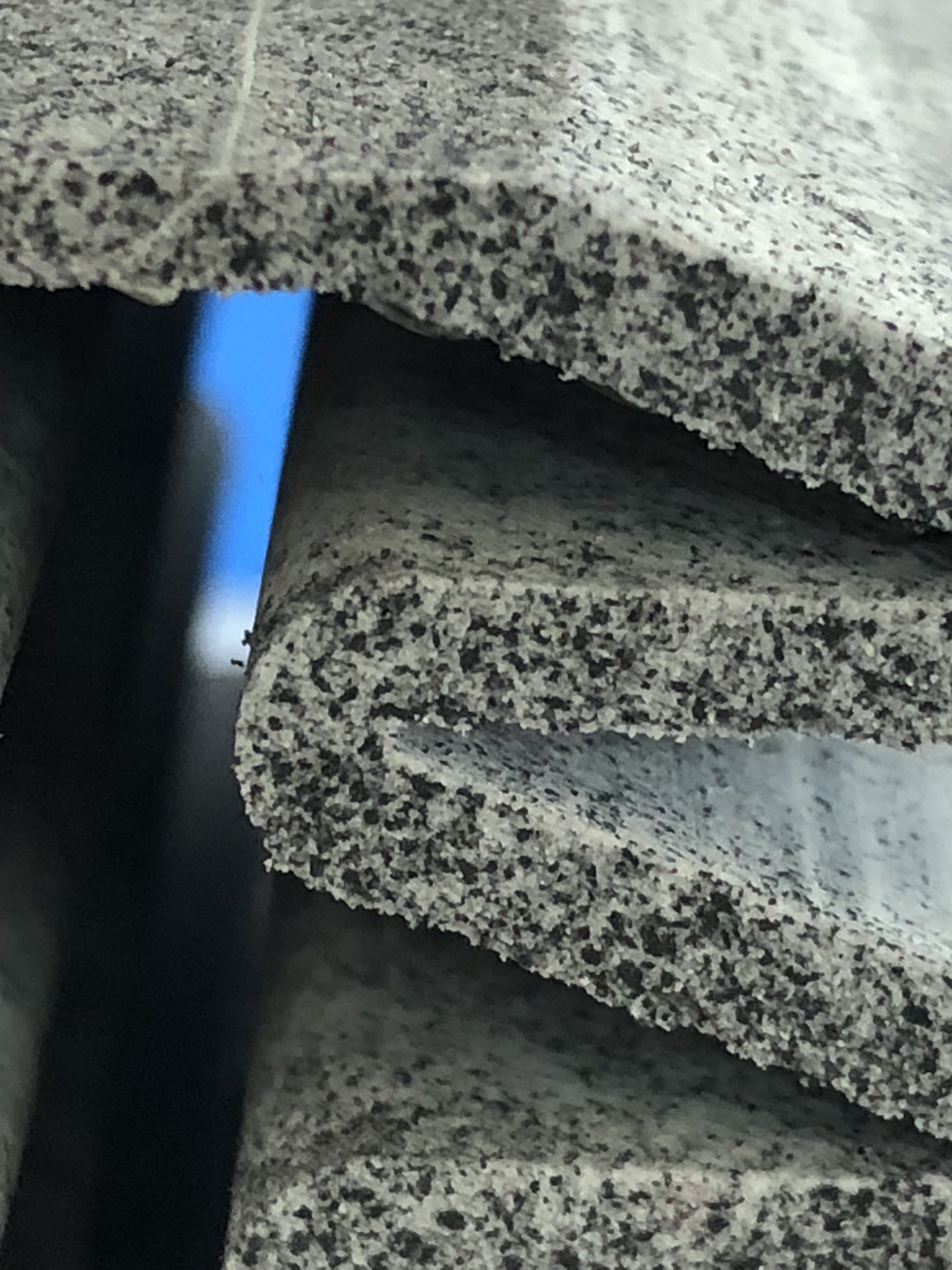
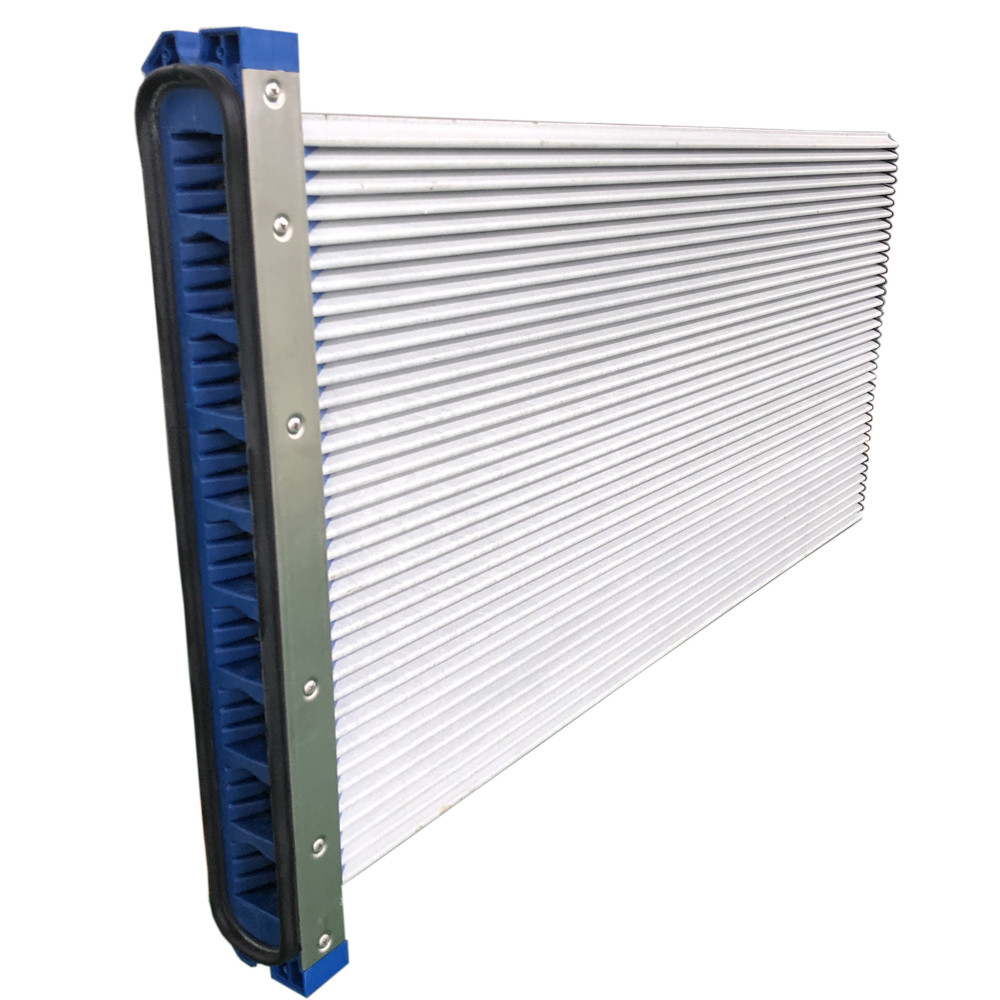
4.Good resistance to static electricity
The surface of the sinter-plate filter is sprayed with a material with good conductivity, and through the integral molding and sintering process, the plastic sintering board has good electrical conductivity. At the same time, the design of the dust collector fully considers the good grounding of the equipment to ensure the safety of the production process.
5.Strong moisture resistance, can be directly washed by water
The base material of the sinter-plate filters and the PTFE coating are completely hydrophobic, and will not produce a water film due to moisture absorption of the fiber fabric filter bag, which will cause a sharp rise in resistance. This is for handling extremely fine iron oxide near the rolling mill under steel rolling conditions has a good effect. The sintering filter can be directly rinsed with water without changing the filter material, which is convenient for equipment maintenance.
6.Long lifespan
The sinter-plate filter is a rigid structure, which eliminates the fiber fabric filter bag caused by the framework wear of life problems. Another feature of long life is the long trouble-free operating time of the filter, which does not require frequent maintenance and maintenance. Good dust removal characteristics will maintain its stable resistance, so that the plastic plate dust collector can work effectively for a long time.The general service life is more than 10 years.
7. Maintenance and replacement is extremely convenient
If the sinter-plate filter needs to be disassembled for cleaning and maintenance, it can be directly pulled out from the support. If taken out from the side of the pulse valve, only the remove the bolts, take out the injection pipe to pull out the sintering filters.
The base material of the sinter-plate filters and the PTFE coating are completely hydrophobic, and will not produce a water film due to moisture absorption of the fiber fabric filter bag, which will cause a sharp rise in resistance. This is for handling extremely fine iron oxide near the rolling mill under steel rolling conditions has a good effect. The sintering filter can be directly rinsed with water without changing the filter material, which is convenient for equipment maintenance.
6.Long lifespan
The sinter-plate filter is a rigid structure, which eliminates the fiber fabric filter bag caused by the framework wear of life problems. Another feature of long life is the long trouble-free operating time of the filter, which does not require frequent maintenance and maintenance. Good dust removal characteristics will maintain its stable resistance, so that the plastic plate dust collector can work effectively for a long time.The general service life is more than 10 years.
7. Maintenance and replacement is extremely convenient
If the sinter-plate filter needs to be disassembled for cleaning and maintenance, it can be directly pulled out from the support. If taken out from the side of the pulse valve, only the remove the bolts, take out the injection pipe to pull out the sintering filters.
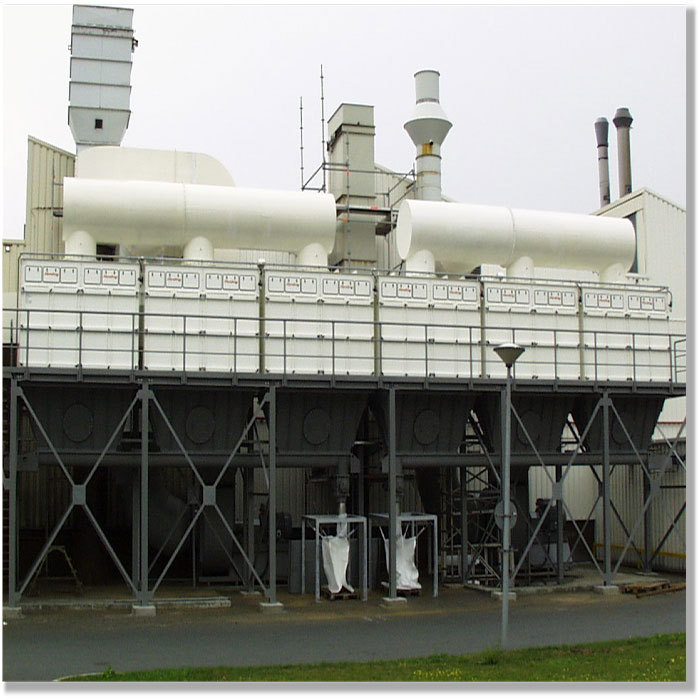
Problems and improvements in the application of sinter-plate dust removal system
The sinter-plate dust collector meets the needs of clean production in the metallurgical industry and is a new technology adopted by the metallurgical industry to achieve cleaner production. However, in the winter climate in the north, a series of problems were revealed in the hot-rolled strip production conditions of the A Steel Plant, and the problems of the B Steel Plant with similar production conditions were not so serious. Through comparison, we put forward the following suggestions on the use of plastic sintered board in the northern hot rolling conditions.
1.Dust treatment near the rolling mill when the dust removal equipment is running:
At the initial stage of equipment commissioning, the production line of Factory A was heavily dusted near the rolling mill. Due to the limited air volume of the fan design and the long pipe length, the suction force at the suction port of the rolling mill is insufficient. In order to improve this situation, through careful observation of the steel rolling conditions of the finishing mill, it was found that the dust collection was reflected in the tailing of the last rolling mill, and there was basically no dust near the first few rolling mills. Therefore, the protection of the dust source of the last two rolling mills was mainly repaired, and the supply of air volume was reduced by reducing the valve opening of the first few air volumes. After the improvement, the dust around the rolling mill was basically eliminated, greatly improving the operation and maintenance environment. The production line of the second plant also uses a shield, and at the same time, water spray devices are added on both sides of the roll, so that a small amount of dust from both sides can enters the trench.
2.Surface area ash due to the shape and injection pressure of the sinter-plate board:
After 3 months of operation of the plastic burning board dust removal system in the production line of Factory A, the fan inlet
2.Surface area ash due to the shape and injection pressure of the sinter-plate board:
After 3 months of operation of the plastic burning board dust removal system in the production line of Factory A, the fan inlet
The air volume is 260,000 m3/h (the design air volume is 320,000 m3/h). At the suction inlet of the rolling mill
After the repairs were made, the dust appeared to be contained, but the air volume still did not increase significantly. Using the maintenance downtime, the surface of the plastic-fired board was inspected, and the surface thickness of the plastic-fired board was found to be 1.0-1.5mm, which was the main reason for the decrease in air volume. The analysis found that the main reasons are as follows: 1 The problem of design selection. That is, the stroke of the compressed air is too long, and the pressure is insufficient, which causes the compressed air to gradually weaken within the range of the stroke; 2Blowing pressure. The design injection pressure is relatively low. If the pressure is increased too much, there will be a load of the components; 3 The shape of the plastic burning board is placed. Plastic burning board is placed horizontally
When one layer of ash falls, a part of it will fall to the next layer. Therefore, vertical placement is more reasonable.
By comparing with the plastic burning board dust collector of the second factory production line, it was found that the overall design of the plastic burning board of the second factory production line was relatively reasonable and the operation was relatively stable. First of all, in the selection of plastic burning board, the effective area is 2 times larger than the production line of the factory A. It uses completely different specifications of the board; secondly, the injection pressure is increased by about 10kP; in addition, the plastic burning board is placed vertically, not The dust from the previous layer falls into the next layer.
3.Condensation and treatment of dust air under low temperature conditions
3.Condensation and treatment of dust air under low temperature conditions
Hot rolling strip production line produces a lot of flue gas during the production process
The dust is mainly iron oxide powder. Due to the need for cooling and lubrication processes in the production process, the flue gas also contains a certain amount of water vapor and oil, and in northern China, as the seasons change, avoid water vapor condensation in the pipeline especially important.
In late autumn, the temperature in the north is low. If the pipeline from the rolling mill to the dust collector is exposed outside the workshop, the plastic burning board has no insulation measures. At low temperatures, water vapor condenses, and a large amount of water will appear in the plastic burning board ash room, and the dust will become a paste. shape.
The production line of Factory A was heated by adding steam to the ash room, and the heat preservation measures were also taken in the pipeline outside the workshop to eliminate the influence of temperature on the dust removal of the plastic burning board. In order to prevent water vapor from attracting people to burn the plastic board, a drain valve is added at the place where the water easily accumulates under the inflection point of the pipeline, which effectively prevents water from being sucked into the ash chamber. The production line of the second factory directly built the entire set of plastic burning equipment in the room, and the use effect is better.
The overall cleaning of the plastic burning board, the thorough cleaning of the dust accumulated in the pipeline, and the restoration of the initial state of the equipment should be done as periodic work.
Conclusion
As the innovative product of powder collection, the sinter-plate powder collector Improvements and innovations will play a greater role in the modern production of the metallurgical industry.